IN A MATTER OF TIME, THAT SCRATCH WILL BUFF ITSELF OUT
BY KATE NG
The Korea Research Institute of Chemical Technology has created a substance straight from the Star Wars universe: an automotive coating that heals itself when exposed to the sun.
According to Korea Bizwire, dynamic urea is a substance that can be added to conventional automotive coatings, giving them the ability to go through the bonding and debonding process repeatedly. In lab settings, a scratch was fully repaired in 30 minutes using daylight, and under 30 seconds with a magnifying glass.
In other words, this is a coating that will regrow and heal all but the most severe cuts ands scratches. While this is among the first cases of regenerating autobody coatings, it is far from the first to create self-healing materials. Enter the world of self-repairing nanotechnology.
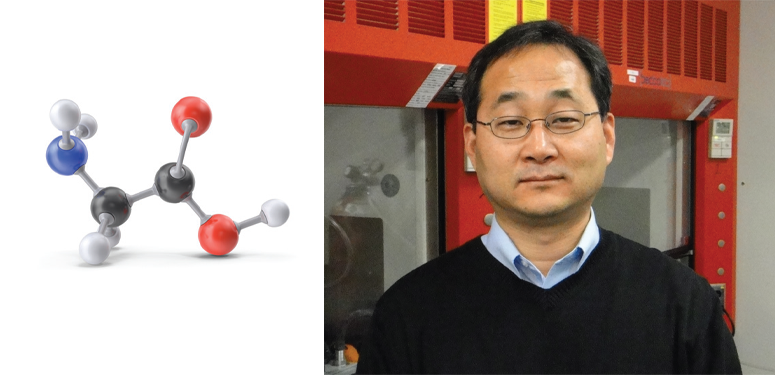
Self-repairing nanotechnology 101
What sets self-healing materials apart from their traditional counterparts is weaker chemical bonds. This allows molecules to break and combine using light or high temperatures, almost like two lumps of chocolate melting on your countertop. Or for an automotive analogy, welding two materials together without the need for welding wire.
Auto body coatings are not the only place that experiments with the technology called dynamic urea bonds. Researchers at the University of Concordia have successfully used dynamic urea self-healing polymers to create a self-healing phone screen. Unlike their Korean automotive counterparts, this can be achieved in seconds at room temperature.
According to John Oh, a supervisor at the University of Concordia’s Laboratory of Polymer and Nanoscale Biomaterials Chemistry, self-healing polymers like dynamic urea are designed with special chemical properties. When the surface is damaged, the damaged molecules chemically deconstruct before they reconnect, using light to activate this healing process.
On a larger scale, this means creating a material whose molecules can selectively adapt their electrostatic force, hardening as a substance or weakening polymer connections to re-establish damaged bonds.
This technology has existed since the 2010s when Nissan created a self-healing autobody coating. While it succeeded as a regenerating coat of paint, it failed as a commercial product. It left marks in healed areas, could not be evenly applied, and cost more to apply than other coatings on the market.
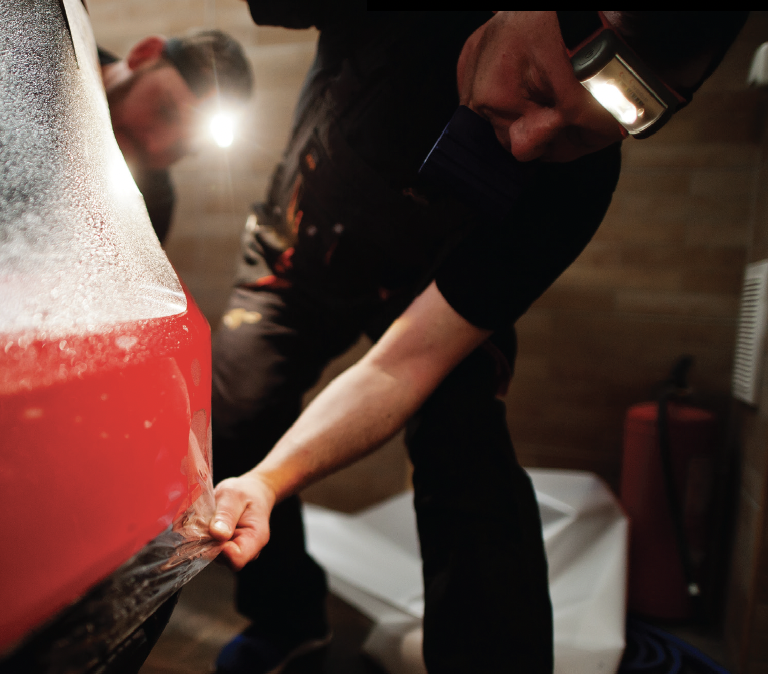
While self-healing materials have found use in the real world as self-healing cutting mats and some (very expensive) autobody coatings, they have yet to truly enter the automotive market at large, primarily due to their high costs of manufacturing and application.
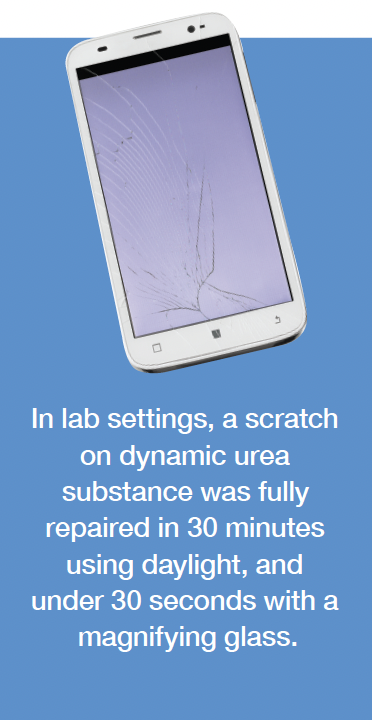
Experimental or Indispensable?
Oh explains that the primary challenge comes from the commercialization process. Experiments in lab conditions highlight the cutting edge of scientific knowledge, but commercial products care about less flashy, but equally important factors. Sustainability, production capability and costs play a role in turning lab technology into commercially available goods.
“The chemistry must be adapted to conditions for commercialization, scaling up from a little sample material to an entire screen,” he said. In the case of dynamic urea materials, Oh emphasizes biocompatibility and processability as particularly important factors—creating substances that won’t poison the user or the environment.
For modern cars, self-sealing components remain the main redundancy measure. Think of multilayered assemblies in fuel tanks and tires that swell to close off punctures. Where these components fall flat is how they are meant to buy the driver time to safely get a replacement part or a serious repair job. Theoretically, this is the niche that self-healing materials could fill.
While self-healing materials have found use in the real world as self-healing cutting mats and some (very expensive) autobody coatings, they have yet to truly enter the automotive market at large, primarily due to their high costs of manufacturing and application. While the technology has been understood, it may take awhile before automotive companies push the funding needed to turn lab-tested concepts into practical, regenerating auto coatings that the average collision repairer or auto body painter keeps in their paint stock.
“It’s hard to say. There’s so much chemistry that can be used, but must be adapted for commercialization,” John remarks.